Casting is a high-precision, low-cost process for manufacturing flexible thin, flat components such as acoustic membranes, battery and fuel cell separators, energy recovery membranes and filtration membranes. In contrast to precision coating, precision casting uses a release coated substrate as a carrier, which is removed before or during assembly of a final product similar to a backing liner on a self-adhesive label.
At Carestream Contract Manufacturing we utilize our experience to help customers determine which of our several dozen coating or casting methods are appropriate for a project. The typical approach to creating high-quality precision products involves “engineering” a fluid to form a free film that is matched to a corresponding coating technique.
Factors such as the number and thickness of layers, porosity or non-porosity, residual solvent level and lamination of protective films or other substrates are critical to the product design. Adjustments, including changes to surface tension, viscosity and solvent mix, are made to match the fluid to a deposition method. We then draw upon previous experience to custom build or tailor equipment for each project.
Technical Considerations for Casting
Casting involves considerations very similar to coating. As discussed in our “Solution Delivery for High Precision Coating” article, precise fluid metering, precision coating heads and tight conveyance tension controls produce coatings with the greatest uniformity. Carestream has invested significant resources in all of these features to ensure product quality for both precision casting and coating projects.
Film thickness and formulation rheology influence the selection of an application method. We customize formulations to achieve highly uniform, pinhole-free films with < 2% thickness variation.
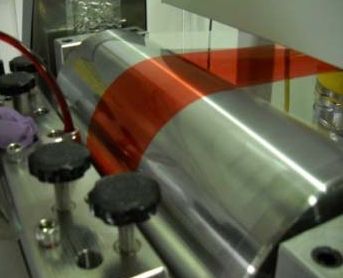
Since cast films are known for their sensitivity to drying, there must be great emphasis on air speeds, temperatures and pressures from zone to zone. Our coating assets have the longest and most precision-controlled ovens in North America, with the flexibility to manage the drying process to eliminate defects such as mud cracking, skinning, blisters, Bénard cells and flow mottle. The option for long residence time in multiple oven zones with different temperatures enables high speeds (and thus low cost), as well as precise control over the drying/curing profile. Independently controlled multi-zone drying is key for applications such as membranes that achieve pore generation via precisely controlled drying of emulsion formulations.
Web conveyance is also important to casting projects. As highlighted in our “Web Conveyance and Roll Winding for Coating Processes” article, the substrate is conveyed through a range of driven and idler rollers; guided past web treatment, coating and/or slitting stations; and then wound onto a master roll. During web conveyance, speed may need to be controlled within a fraction of a percent for precise treatment or coating uniformity. Active tension control is required to maintain traction with the idler rollers and avoid scratching, stretching, tearing, wrinkling and creasing. Process conditions and machine hardware must match the web characteristics.
End Uses for Casting Applications
Carestream has experience casting acoustic membranes, haptic membranes, fuel cell membranes, battery separators, water treatment membranes, filtration membranes, ceramic “green tape” casting, energy recovery membranes and beyond. Some products are multi-layered. For example, filtration membranes have different size pores at various levels of the membrane, which require the use of slightly different polymers and curing profiles.
Other examples include ceramic tape casting, used in the construction of films that are subsequently “fired” to volatilize all organic materials in the casting formulation and produce a ceramic structure. Ceramic chip capacitors are made this way, with alternating layers of copper and green tape; the green tape is solvent dried, but not fired. Casting a green tape with an acrylic polymer binder and water is common and highly precise with good economics. The tape is easy to work with since it is on a carrier substrate. This method produces a pinhole-free, semi-dried material that can be stacked into a capacitor or other ceramic, metal or polymer structure.
Carestream fabricates thin, flat components for high-temperature fuel cells as well, including structures such as solid oxide fuel cell “stacks” (SOFCs). We process the materials to cast SOFC membranes and coat multiple layers of ceramic particle slurries. Creating multi-layer structures in a single processing step often eliminates the need for subsequent processing steps and increases yield.
Carestream has the expertise and knowledge to deliver a precision casting process that meets your product’s requirements and enables commercial production. This can be done using a rapid prototype to production process that is cost-efficient and minimizes time to market. Please contact us to discuss your processing needs.