Simultaneous, Precision Multilayer Coating Expertise
Carestream’s simultaneous, precision multilayer coating technology and manufacturing expertise can be leveraged for a variety of precision coating and cast film applications. Our multilayer slide coating dramatically reduces production time by enabling simultaneous coating of ≥ 2 film layers in one pass. It also provides the design freedom to improve product performance with additional layers, and allows higher line speeds, reducing coating cost compared to slot die coating.
Our ability to coat complex products is demonstrated by what we do with Carestream DRYVIEW Medical Laser Imaging Film. The six-layer film product contains over 25 different components, including nanoparticles. It features four simultaneously-coated layers on the top of a PET film base and two simultaneously-coated layers on the bottom side of the PET film, with all six layers coated in a single pass through the machine. Millions of square meters of Dryview Medical Laser Imaging Film are coated every month to meet the stringent requirements of an FDA-regulated Class 1 medical device, proving our ability to tackle even the most challenging coating projects.
Due to Carestream’s history of innovation in precision multilayer coating technology, we offer expertise with a wide range of coating technologies, including multilayer slide (cascade), multilayer slot die and multilayer curtain coating to allow for a range of value-adding multilayer design possibilities. Learn more about each of these coating methods below.
Multilayer Slide Coating: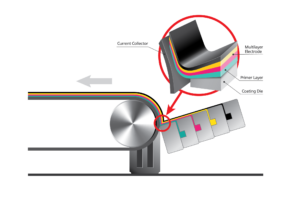
- Delivers lower cost by enabling the simultaneous coating of multiple layers at higher line speeds than slot die.
- Allows the design freedom to improve performance with additional layers at no added coating cost.
- Reduces waste with fewer passes through the coating machine.
- Enables a wide range of wet and dry thicknesses, both per layer and for all layers in total.
- Numbers of layers: 2 to > 5.
- Very high layer and total uniformity.
Multilayer Slot Die Coating: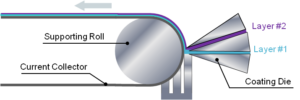
- Ensures lower-cost coating via the ability to simultaneously coat multiple layers.
- Reduces waste with fewer passes through the coating machine.
- Enables a wide range of wet and dry thicknesses.
- Number of layers: 1 or 2, with possibility of 3.
- Very high layer and total uniformity.
- Good coating line speed.
- Lane coating and patch coating.
Multilayer Curtain Coating: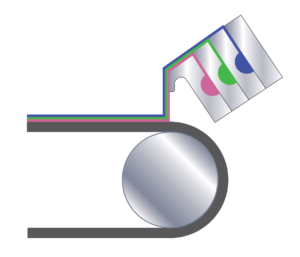
- Delivers lower cost by enabling simultaneous coating of multiple layers at extremely high line speeds.
- Allows the design freedom to improve performance with additional layers at no added coating cost.
- Reduces waste with fewer passes through the coating machine.
- Enables a wide range of wet and dry thicknesses, both per layer and for all layers in total.
- Numbers of Layers: 2 to > 10.
- Very high layer and total uniformity.
Read our multilayer coating case studies below to find out more about our coating innovation, or contact us to learn how our multilayer coating partnerships deliver a competitive advantage for developing a wide range of product applications.
DRYVIEW Medical Laser Imaging Film Case Study
Challenge:
A valuable and growing product required greater capacity and lower cost.
- The product required multilayer coating (MLC) but line speed was limited by dual slot die coating.
Solution:
- Multilayer slide coating process developed.
- Re-engineered dispersions for multilayer slide process; added layers to enable process change.
- Designed new equipment to support high speed MLC: solution delivery, slide coater, ovens.
- Overcame challenging product/process interactions and provided robust layer integrity, coating stability, uniformity and quality.
Results:
- Increased line speed and therefore capacity by > 4X.
- Reduced cost dramatically.
- Improved uniformity, quality and yield.
- Enabled differentiation and supported rapid growth of the product in the marketplace.
- Delivered exceptional earnings to the corporation.
- Design freedom allowed additional layers that improved product performance and productivity.
Optical Film Case Study
Challenge:
- A multilayer construction with unique optical properties required precision coating.
- Expensive substrate required very high yield to meet economic goals.
- Individual layer coating could not maintain the required precision.
Solution:
- Multilayer slide coating process developed.
- Re-engineered dispersions and solutions for multilayer slide process.
- Designed new equipment to support high speed multilayer coating: solution delivery and slide coater.
- Designed new process in one coater pass taking advantage of two coating stations.
Results:
- Attained above target yield of expensive substrate.
- Maintained high precision required of individual layers and total construction.
- Surpassed cost goals by high yield and one machine pass process.
Functional Medical Film Case Study
Challenge:
R&D developed a three layer construction to address multiple requirements in a medical application.
- Multiple machine passes added too much cost and yield loss to the product.
- Primer layer defects could not be detected until coating subsequent layers.
Solution:
- Multilayer slide coating process developed.
- Re-engineered dispersions and solutions for multilayer slide process.
- Designed new equipment to support high speed multilayer coating: solution delivery, slide coater and ovens.
- Overcame challenging product/process interactions and provided robust layer integrity, coating stability, uniformity and quality.
Results:
- Eliminated additional coater machine passes.
- Increased line speed vs. highest speed single layer.
- Reduced cost dramatically through higher speed, fewer machine passes and reduced waste.
- Increased yield by eliminating machine passes and ability to validate the entire construction quality at time of initial coating.