Web or substrate conveyance through coating or converting machines can be filled with an assortment of challenges, involving a long list of contributing factors. The substrate needs to be conveyed through an array of driven and idler rollers, guided past web treatment, coating and/or slitting stations, and then wound into a master roll. During web conveyance, speed may need to be controlled within a fraction of a percent for precise treatment or coating uniformity. Active tension control is required to maintain traction with the idler rollers and avoid scratches, stretching, tearing, wrinkles and creases. Success requires matching process conditions and machine hardware to the web characteristics; failure to do so would be akin to driving a monster truck on a putting green.
Web Conveyance
Substrate properties should be considered first when determining and optimizing conveyance set-up for the web material, whether it be paper, film or foil. These values are sometimes available from the supplier or can be measured in the lab. Some of the most critical factors for optimal web conveyance include:
- Tensile Strength: The tensile strength is the maximum stress or force per unit area that a material can withstand while being stretched or pulled before failing or breaking. The substrate strength may change after a coating is applied, especially for papers that absorb liquid, weakening the fibers.
- Tear Strength: Tear strength is how well a material resists the growth of cuts or nicks while under tension. Some materials tear easy like thin papers. Others are so tough they will bend rollers and break shafts before the web breaks. The addition of a brittle coating can sometimes decrease the web’s tear resistance.
- Dynamic Coefficient of Friction between the Web Material and Roller Surfaces: At speed air flotation may occur at low tensions and/or higher speeds depending on the surface finish of materials and rollers. Loss of traction causes scratches, guidance and drive control issues.
- Web Planarity and Camber: No web is perfectly flat or straight, and the conveyance process must deal with these variations.
- Edge Curl: Some substrates will curl at the edges when under tension or when wet from a coating solution. This curl can cause guiding challenges and may increase the risk of a web break.
The process parameters that need to be considered in light of these substrate properties include:
- Line speed, which is often set by the coating and drying limits.
- Tension, usually measured in force per linear width. The tension throughout the web path should typically be set between 10% and 25% of the substrate’s tensile strength to keep it taut and provide sufficient traction over rollers without stretching or breaking.
- Drive tuning for good response depending on web speed and tension upsets.
- Machine acceleration rates since rates that are too high may cause tension issues.
- Air pressure in dryer or air conveyance sections, because air blown on the web may cause guidance issues if web catenaries are too deep between rollers. These pictures show how adjusting web tension and air pressure reduces creasing on a thin substrate:
Before After
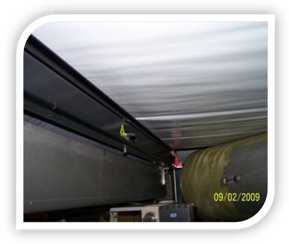
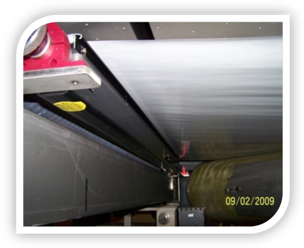
- Vacuum levels on drive rollers that are ported to improve traction. If vacuum levels are too high, they may cause creases; if they are too low, the web may slip.
- Condition monitoring to alarm upset conditions.
Conveyance equipment should be inspected to ensure that the hardware is functioning to optimal performance. Adjustments to key machine hardware may improve web-handling robustness dependent on the substrate properties and process parameters. Below is a sampling of properties to look for when determining whether modifications or replacement of key hardware is required.
- Roller Stiffness: The roller stiffness is dependent on diameter, wall thickness and material.
- Roller Traction: Roller traction is dependent on the surface finish, which may be smooth, elastomeric covered, sand blasted, etched or grooved.
- Roller Profile – Straight Cylinder, Bent or Concave: Bent and concave rollers are used for web spreading to avoid creases or to provide a flat web for a specific process. These pictures show how changing the roller profile eliminates creasing on a thin substrate:
- Roller Drag: The roller drag minimizes with the size and type of bearings, lubrication and seals.
- Roller Inertia: If the machine starts and stops, high-inertia rollers may cause tension variations and creasing or roller slippage and scratches.
- Roller Alignment: Alignment typically maintains parallelism within the thickness of web and across the width of web.
- Web Spans between Rollers: Spans that are too long may allow the web to form draw lines, like folds in a curtain, and cause creases.
- Drive Control: Power and speed control capability with master and slave drives requires good speed feedback and drives strategically located along the path to minimize the tension range through the machine. Tension models are available, which use web bending forces, air and bearing drag, web elevation changes, and roller inertias.
- Tension Control: The system to measure tension in web for drive feedback can be float roller, back pressure or load cell device.
- Guiders: Guiders are needed to correct and position web tracking due to variances in web camber, planarity and roller alignment. Trimmer guiders may be required very close to coating, treatment or scanning stations.
Roll Winding
After the web is conveyed, coated, dried and/or converted, it is then wound into a master roll for shipment to the customer or transfer to a subsequent converting operation. Roll winding also requires consideration of the substrate, process and equipment interactions to avoid problems such as buckles, creases, corrugations, lap impressions, shifting, and baggy or rough sidewall on rolls. The most critical factors to consider during the roll winding process include:
- Web Stiffness: As stiffness decreases, the substrate is more prone to creasing.
- Web Thickness Uniformity: Thicker lanes in the web may cause ridges or hard streaks and localized pressure in wound rolls.
- Web Elasticity: Webs that stretch may cause high inner lap roll pressures that can crush cores or deform bottom layers. Non-elastic webs such as paper may be wound harder without issues.
- Coefficient of Friction of Web Face to Back: If the coefficient of friction is too low, it may cause rolls to telescope during winding or transport.
- Web Planarity or Bagginess: If the roll being wound has web planarity or bagginess, centerline creasing or diagonal creasing may occur on one or both edges.
- Core Stiffness: If a roll is end supported, the core must be strong enough to avoid deflection during the wind that may cause centerline creasing. Weak cores can also lead to buckling or collapse of full-size rolls.
- Web Edge Design: Knurled edges can reduce inner lap pressures and increase roll stability.
- Edge Coating Effect: A thick coating edge bead may cause thickness issues and ridges in a wound roll.
While there are fewer process conditions to consider for winding than for conveyance, they can be just as critical. Speed and tension are the major factors for winding. High velocities will require higher torque and may entrain air between layers. Good tension control will provide more uniform winding. Tension that is too high may cause creasing or stretching of the web. Web tension may be tapered or decreased as the diameter of the roll increases to reduce torque at the core and propensity to shift or telescope. These pictures show how adjustments to the winding tension reduce creasing:
Before After

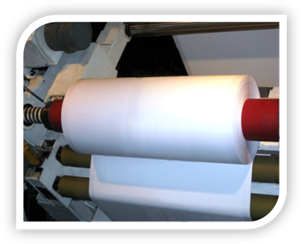
As with web conveyance, modifications to the winder hardware design may be necessary when the substrate properties or process parameters are significantly different from existing products. Factors for determining the need to modify or replace the winder hardware include:
- Spindle Design: Delivers the ability to chuck cores of required inside diameter and provides winding torque through the core without tearing it.
- Center Shafts: These shafts support weaker cores during winding.
- Surface Wound Winder: The surface-wound winder should support the roll on the outside diameter if no core is used or for very thin cores.
- Pressure Roller: Pressure rollers squeeze out entrapped air between winding layers for increased speed, better sidewalls and roll integrity.
- Power, Torque and Size: The winder hardware must have the power, torque and size to handle the winding tension, web width, diameter and weight of the master roll.
- Web Guiding: The web guide positions the web so that it is centered on core with good sidewall uniformity. A guider positioned just before the winder provides better control than trying to steer a heavy winder to the incoming web.
- Spindle Alignment: Proper spindle alignment avoids shifted roll issues.
Conclusion
Both web conveyance and roll winding require the consideration of many factors and involve a spider web of interdependencies to create a robust process and optimum product. Carestream Contract Manufacturing has over 100 years of legacy experience in web handling for widths from 0.5 to 74 inches, thickness from 1 to 12 mils, speeds of up to 3000 fpm, and roll lengths of up to 30,000 feet. The substrate testing capabilities of Carestream’s Coating Assessment Lab and the technical experience of its engineers provide significant quality, development speed and cost advantages to customers bringing new, coated products to market.